新竹汽車報廢流程的問題,我們搜遍了碩博士論文和台灣出版的書籍,推薦蕭瑞麟寫的 讓脈絡思考創新:喚醒設計思維的三個原點 可以從中找到所需的評價。
國立金門大學 管理學院事業經營碩士在職專班工業管理組 呂立鑫、江育民所指導 辛鴻慶的 六標準差DMAIC與TRIZ方法應用於製程改善之研究-以製酒業包裝製程為例 (2021),提出新竹汽車報廢流程關鍵因素是什麼,來自於DMAIC、TRIZ、製程改善、製酒業、包裝製程。
而第二篇論文國立成功大學 工業與資訊管理學系碩士在職專班 黃宇翔所指導 余曜宇的 應用實驗設計進行半導體晶圓去膜製程最佳參數之研究 (2020),提出因為有 去膜製程、因子實驗設計、反應曲面法、參數最佳化的重點而找出了 新竹汽車報廢流程的解答。
讓脈絡思考創新:喚醒設計思維的三個原點
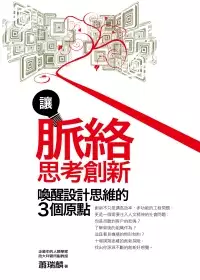
為了解決新竹汽車報廢流程 的問題,作者蕭瑞麟 這樣論述:
創新來自創舊?為什麼創新沒有脈絡就會失敗? 脈絡,就像中醫的診斷原理。頭痛,往往要醫腳,因為你看到的問題常常只是徵兆,而不是病因。了解脈絡就是一探事出之因。由過去發生的事,解釋現在的問題,再向前推測未來的發展軌跡。 為了釐清創新的脈絡,作者蕭瑞麟以企業中的人類學家自許,帶領團隊近身觀察、感受田野,深入探訪各類組織在進行或導入創新時,成功(或失敗)背後的故事。 頂尖科學家與研發團隊的養成,如何來自三個教授的刻意修練? 從半導體的機台維修,看看現場工程師如何由物件推理,找到根本問題。 別讓哈佛變哈欠。別只模仿人家的創新,要學會「偷」創新,融入自己的特色! 作者將帶領讀者重回
創新事件現場,抽絲剝繭,尋找別讓創新成為遺憾的解答。創新不只是講高效率、多功能,更需要注入人文精神:你是否聽到客戶的悲鳴?了解背後的組織作為?並且看見機構的無形制約?當讀者從脈絡學會思考,喚醒了感覺,就能設計出令人感動的創新。 請跟著這位充滿好奇心的質性研究者進行一趟創新歷險,挖問題,解問題,思考自己碰到的創新問題。 作者簡介 蕭瑞麟 現任國立政治大學科技管理研究所副教授,並於新加坡國立大學負責亞太高階主管EMBA之「資訊與決策」課程。研究領域包括資訊科技與組織變革、科技創新、跨域知識整合與供應鏈管理。經常參與跨國公司在亞洲的創新專案,如Rolls Royce、Ernst &
Young、Singapore Technology Engineering、DHL、Nokia等。他是質性研究領域的中生代學者,目前擔任Information Systems Journal 執行編審、Academy of Management (Learning & Education)、Computers in Human Behaviors 編輯委員、中山管理評論編輯委員等職。他的著作常見於國際性會議與期刊,並屢次得獎。他的個案研究以追溯科技背後的組織病理為特色,常用輕鬆活潑而又懸疑的辯證手法呈現科技創新的挑戰。他創新的教學方法亦榮獲新加坡國立大學「EMBA最佳教師獎」。其近作
《不用數字的研究》以淺顯易懂的方式介紹艱澀的研究方法,該書被選為臺灣科管百大優質叢書,亦列於年度最佳暢銷書之一。
六標準差DMAIC與TRIZ方法應用於製程改善之研究-以製酒業包裝製程為例
為了解決新竹汽車報廢流程 的問題,作者辛鴻慶 這樣論述:
國內白酒產業近幾年受到中國大陸禁奢政策、進口烈酒、酒駕法、飲酒文化、疫情肆虐等因素的影響,要在銷售開源尋求重大突破恐不容易,企業必須做好節流工作,減少營運負擔。案例公司的半自動化包裝線,負責包裝種類繁多的酒品,製程工序、手法較多且複雜、人工作業比例高,因此,生產製程良率相對也較差,會產生較多的重工與報廢成本,對公司是一種負擔。本研究即以改善案例公司的包裝製程良率為議題,應用六標準差DMAIC架構和TRIZ方法的結合,針對個案公司所生產的產品,做包裝製程良率的改善。依照DMAIC的改善步驟,並融入QC工具,找到影響良率的核心問題,並分析背後潛藏的原因,最後導入TRIZ的工程參數、矛盾矩陣、發明
原則工具,希望能在短時間,完整的構思出有效益、節省成本的最佳改善方案。經過個案的研究與驗證,順利找到造成該產品包裝製程不良的關鍵問題,有效降低製程不良率。在「貼小標、防偽標不良」的改善方面,構思出改善電眼感應設置,降低貼標不良率幅度達56%。在「破瓶」不良的改善方面,則找到取放瓶與充填機配合速度的參數設定,並以鐵片當作橋樑來銜接目檢工站與貼標工站兩段輸送帶間之斷差,可降低破瓶不良率幅度達89%。另外,亦從設計面提供取消小標、防偽標與封套結合之建議方案,供個案公司評估參考,可完全解決貼小標的不良問題。本研究證實六標準差DMAIC架構搭配TRIZ的創新思維模式,對製酒業包裝製程的改善及問題的解決,
的確能簡便、迅速、全方位的激發出合適的對策。
應用實驗設計進行半導體晶圓去膜製程最佳參數之研究
為了解決新竹汽車報廢流程 的問題,作者余曜宇 這樣論述:
為了滿足近年來虛擬實境 (Virtual Reality ; VR) 、虛擬貨幣挖礦 (Mining)、自動駕駛汽車、人工智慧 (Artificial Intelligence ; AI)、5G通訊(5th Generation Mobile Networks)等需求大量高速資料運算晶片(Chip)的相關市場,在不增加產品體積又必須達成高速運算的前提之下,客戶端需求在固定的積體電路 (Integrated Circuit ; IC)空間內堆疊更多的晶片以達成高密度封裝。因此客戶所需求的晶圓(Wafer)研磨厚度也愈來愈薄,研磨後的超薄晶圓非常的脆弱,對後續封裝製程高良率的維持形成一大挑戰。
本研究主要探討晶圓研磨薄化中的去膜製程 (De-taping)。去膜製程的主要任務是將晶圓晶背研磨前,於上膜 (Taping) 製程中在晶面貼上的晶背研磨保護膠膜 (Back Grinding Tape ; BG Tape) 撕除。由於晶圓研磨薄化後的厚度低於保護膠膜的厚度,且因不同產品的晶面電路佈線設計不同,導致上膜後膠膜附著於晶面的黏著度不同。上述問題造成去膜機的去膜手臂 (Peeling Arm) 時常於去膜初期將晶圓前端拉起或將晶圓拖曳位移,進而導致去膜平台真空吸附值低於警戒設定值觸發機台機故,嚴重狀況甚至造成晶圓受損報廢。在設備機台方面,影響去膜成功與否的參數因子水準眾多。因此
本研究利用特性要因圖,找出機台中可能導致去膜失敗的因子,接著利用DOE (Design of Experiement ),執行部分因子實驗設計,記錄應變數之數值,並執行二階段反應曲面設計實驗,找出去膜最適參數組合以減少去膜失敗次數,以改善去膜製程良率。實驗結果發現機故率由原本平均40%大幅下降至15%,過往該產品平均作業20片會有8片晶圓於去膜時被手臂拉起。透過最佳參數組合,執行20次驗證實驗,發現僅有3片在做作業時被拉起,作業平台前端真空平均值也由77.6千帕提升至80.32千帕,最佳化參數實驗結果相較於原作業狀況改善許多。