產品 生產流程的問題,我們搜遍了碩博士論文和台灣出版的書籍,推薦吳永富寫的 圖解單元操作 和喬治‧史托克(GeorgeStalk,Jr.),湯瑪斯.郝特(ThomasM.Hout)的 時基競爭:快商務如何重塑全球市場都 可以從中找到所需的評價。
另外網站2.1 產品生命週期管理需求 - 政大機構典藏也說明:全球化的市場競爭下,對企業最大的影響莫過於業務流程的改. 變。首先面臨的即是產品的研發,再來是從訂單取得,到涉及原料的. 備料、生產流程等程序,然後是物流管理 ...
這兩本書分別來自五南 和經濟新潮社所出版 。
逢甲大學 綠色能源科技碩士學位學程 賴奇厚所指導 曾心妤的 以生命週期評估分析臺灣有機柑橘園的碳排放與經濟效益 (2021),提出產品 生產流程關鍵因素是什麼,來自於碳足跡、碳排放、生命週期評估、碳價比、價碳比。
而第二篇論文修平科技大學 精實生產管理碩士班 陳義分所指導 王詠薇的 精實管理之價值溪流圖分析在半導體封裝製程之改善應用 -以S公司為例 (2021),提出因為有 精實管理、價值溪流圖、半導體封裝、SMT製程的重點而找出了 產品 生產流程的解答。
最後網站企業流程改善分析-以慶興公司為例 - 建國科技大學則補充:SWOT 分析、有效的生產管理製程分析、接單及進出貨管理分析、品管作業分. 析、產品開發作業分析,使生產線上的工作環境、生產流程以及人員配置的整. 個工作系統能更有效率 ...
圖解單元操作
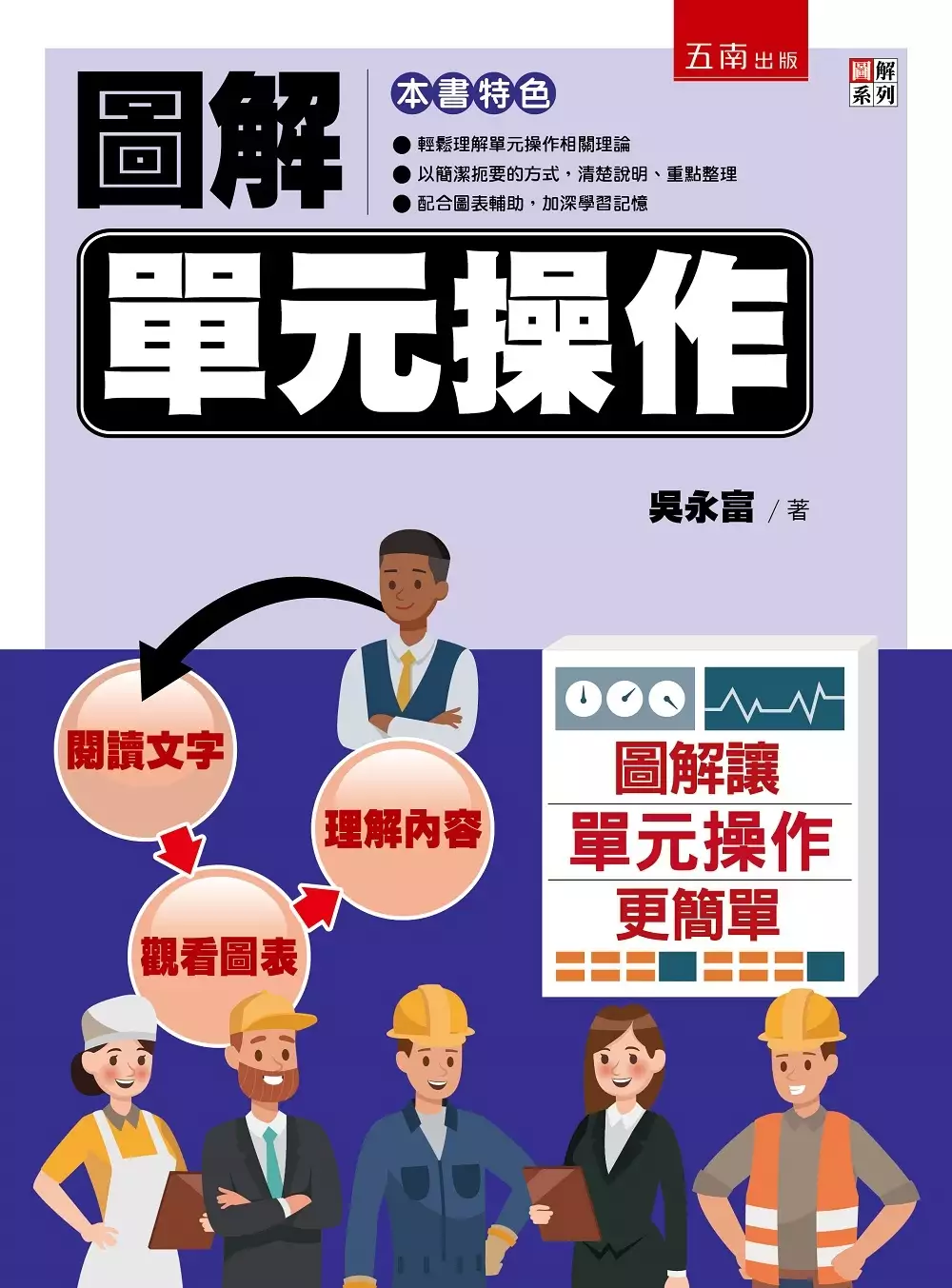
為了解決產品 生產流程 的問題,作者吳永富 這樣論述:
工廠中一系列的製造流程可以被拆解成小單元,分開的個別程序被稱為單元操作。每一種單元操作皆可視為原料輸入再形成產物輸出的程序,在各式各樣的生產流程中,只要基於相同的機制,皆代表同一類單元操作,唯有其規模不同。 工程師在生產技術的發展中扮演重要角色,尤其面臨新製程之設計時,往往只知道原料與產品,對於反應器、產品分離方法、操作條件等議題,皆有待思索,因而需要進行單元操作的設計。之後再思考整體程序,期望能減少步驟,改進個別操作之效率,尋找最適化的流程,最後再將規模放大,從實驗室推廣到試驗廠,再擴大到量產廠。工程師必須整理與研判各種構想和訊息,重複利用單元操作的概念,採用最經濟與最安全的
程序,以建廠製造出產品。單元操作的對象可依物質狀態分為固體、液體和氣體,有時也包含超臨界流體,這些物質必須被輸送、加熱或冷卻,而且需要經歷混合與分離,因此牽涉動量、熱量與質量之輸送。掌握了單元操作的概念,即可奠定工業生產的基礎。本書扼要介紹混合與分散、多相分離、均相分離等單元操作,並闡述其原理、延伸和應用,可作為工程科系學生快速理解製程領域的入門資料。
產品 生產流程進入發燒排行的影片
福特六和汽車自 2016 年即著手進行 5 年內超過新台幣 40 億元的在台投資計畫,實現生產設備更新、生產流程智慧化以及新產品計畫。在與配合的供應商以及政府共同推動這項專案之後,福特六和於 2017 年開放了媒體進廠參觀,讓國內消費者初步了解擁有 48 年歷史的福特六和中壢製造廠的設備更新與優化。經過四年的時間,這項專案已在近期完成目標,並再度邀請媒體前來一同了解 Ford 在品質上的要求及生產設備升級的成果。
延伸閱讀:https://www.7car.tw/articles/read/71223
以生命週期評估分析臺灣有機柑橘園的碳排放與經濟效益
為了解決產品 生產流程 的問題,作者曾心妤 這樣論述:
全球由人類管理的最大生態系統是農業,仰賴外來資源與維護大面積單一作物為主要耕種方式,促使溫室氣體的排放量增加和生物多樣性下降。碳足跡是衡量一項活動或產品的整個生命週期中直接或間接排放積累的溫室氣體,是各國政府及企業達成溫室氣體減量目標的工具之一。本研究使用生命週期評估法分析台中市東勢區的有機柑橘,以及有機柑橘加工製成柑橘果醬,還有以柑橘果醬製成精釀啤酒的碳排放情形。透過實地盤查及訪談取得相關資訊及數據,計算自原料取得階段、產品製造階段、銷售配送階段、消費者使用階段至廢棄處理階段之碳排放量,分析排放熱點進行減量評估。有機柑橘種植分別依照(1)盤點年度實況(適逢旱災減產)、(2)未逢重大災害、(
3)慣行農法栽種(使用化學肥料)三種情境進行碳足跡計算及分析,結果顯示氣候變遷導致果樹減產對於碳排放量的影響最甚,有機耕作除了減少溫室氣體的排放,更間接產生保護環境、維護生態平衡的積極作用。柑橘果醬的主要排放熱點為產品製造階段使用液化石油氣,若能善用果園每年夏、秋二季整枝修剪的木材作為燃料,可以降低49.9%的碳排放量。精釀啤酒製程的排放熱點為(1)玻璃瓶、(2)能源使用、(3)原料運輸,以使用回收玻璃瓶、購買綠電憑證、使用國產麥芽等策略,降低原生產程序58.5%的碳排放量。本研究參考本益比及性價比概念,提出碳足跡與收益淨利或成本支出相關聯的評估指標-碳價比及價碳比。在初級農產及加工加值過程中
,柑橘果醬的碳價比(0.0037 kg CO2e/元)較有機柑橘(0.004 kg CO2e/元)及精釀啤酒(0.0068 kg CO2e/元)來得低,柑橘果醬使用不具市場價值的次級柑橘作為原料,不僅減少食物浪費,更賦予原先無法販售的產品新價值,提升經濟效益。精釀啤酒的價碳比(133.7 元/kg CO2e)較有機柑橘(104.8 元/kg CO2e)及柑橘果醬(35.28元/kg CO2e)來得高,表示精釀啤酒投入的每單位成本產生的碳排放量較少,具有相對高的減碳效益。在小農經濟的型態下,透過地方創生盤點各地核心元素,結合六級化產業的推動,是提升農民獲利的關鍵方向,透過異業合作打造特色加值農產
創造行銷效益,提高農業附加價值,輔以產品碳標籤的申請,使消費者透過經濟活動支持友善環境且低碳的產品,促進生產者以低碳方式進行生產。
時基競爭:快商務如何重塑全球市場

為了解決產品 生產流程 的問題,作者喬治‧史托克(GeorgeStalk,Jr.),湯瑪斯.郝特(ThomasM.Hout) 這樣論述:
暢銷30年的策略經典,首度出版繁體中文版 蘋果(Apple)執行長提姆‧庫克(Tim Cook)推薦員工必讀的一本書 速度是競爭的本質, 以戰代練、提升實力、縮短流程, 學會和時間賽跑,你就是後疫情時代的大贏家! 在快速變遷的時代,決定勝負的關鍵不再是企業的規模大小,而是企業應變及超前布局的速度,疫情更強化這個趨勢。 這本書出版於1990年,是暢銷30年的策略經典。二位作者是波士頓顧問公司(Boston Consulting Group,BCG)高級顧問喬治‧史托克(George Stalk, Jr.),以及顧問經驗超過三十年的湯瑪斯.郝特(Thomas M. Hout)。
他們在1980年代研究當時的日本企業如何超越美國,發現日本企業勝出關鍵在於速度,也就是縮短產品開發和生產流程。當時,企業通常比的是規模大小,必須衝到業界第一大或第二大,否則無法生存。 因此,他們提出大膽的想法,也就是勝出的關鍵在於速度,而不是規模。即使公司規模再大,如果因應變化的速度太慢,就可能遭到淘汰。 「以時間為基礎的競爭」(簡稱為時基競爭)不只是1990年代的思維,後疫情時代更是明顯,能夠挺過疫情、表現亮眼的企業,都能快速滿足客戶需求。但是,追求快速並不等於「零犯錯」,沒有錯誤表示不敢做決定,反而可能減緩速度、削弱競爭力。企業要有一定的容錯空間,就算出錯,也能存活而且變得更好。 各
行各業都可以重新思考,如何將「追求速度」納入日常管理。無論你所屬的公司是服務企業(B2B)還是個人(B2C),不一定要規模大才能賺錢,只要速度夠快也能獲利。追求速度不只可以賺到錢,也能夠很快滿足客戶的需求,提供客戶更多的商品或服務。 規模大小,已經不是基業長青的保證;追求速度,卻能讓企業可長可久。想要在後疫情時代勝出,必讀這本策略經典! |導讀| 徐瑞廷|波士頓顧問公司(Boston Consulting Group,BCG)董事總經理暨全球合夥人、BCG台北辦公室負責人 |一致推薦| 何英圻|91APP董事長 林啟峰|富邦媒(momo)董事長
精實管理之價值溪流圖分析在半導體封裝製程之改善應用 -以S公司為例
為了解決產品 生產流程 的問題,作者王詠薇 這樣論述:
精實生產管理主要爲流程合理化改善活動,其目的是協助企業精簡製造流程、降低產品成本、提升生產力,以增加產業的競爭力。精實生產既是一種以最大程度地減少資源浪費降低企業生產運營成本為主要目標的生產方式,同時也是一種理念和文化。它可以靈活地適應各種行業不同類別產品的生產工藝和管理技術,無論對大量生產或小批量製造業具有積極的意義。本研究以「精實生產管理」理論,有系統地建立精實生產模式導入某半導體封裝製造公司進行實務驗證,結果顯示精實生產的導入對該公司有顯著的效益。精實生產管理藉由價值溪流圖 ( Value Stream Mapping ) ,將生產製程繪製成一示意圖表,可以明確表示物流、資訊流及生產作
業時間的圖表,在圖示化後,可讓管理人員很容易的分析流程中,生產流程中現況衍生的浪費根源而加以進行改善。本研究過程中運用價值溪流圖做為切入點,重新確定其生產作業產品在半導體封裝業中,SMT( Surface Mount Technology簡稱為SMT)製程中的動作價值,依據現況流程去除没有價值的動作,確保產品在製程的流動暢行無阻、提高生產效率,最後再繪畫出未來價值流圖,做為持續改善達到人力的節省、縮短交期、降低在動作浪費的目標,達到最大的效益,並依此實施並展開有效的改善計劃。
產品 生產流程的網路口碑排行榜
-
#1.生產規劃佐理員
生產規劃人員會恨據客戶訂單的產品規格、數量與交貨期,並考慮工廠現有的設備、人方、生產線,毫不浪費且期望達到最高的生產效能,來規劃出最適切的生產流程,並安排出每一 ... 於 w3.tpsh.tp.edu.tw -
#2.與時俱進生技資訊系統生產管理銷售全透明 - 台糖公司
事業部成立至今已將近15年因應生產流程、法規及業務需求更迭,期間各系統經過整併 ... 進銷存管理系統(NSL),負責產品銷售及管理,事業部屬生產單位對於產品生產流程 ... 於 www.taisugar.com.tw -
#3.2.1 產品生命週期管理需求 - 政大機構典藏
全球化的市場競爭下,對企業最大的影響莫過於業務流程的改. 變。首先面臨的即是產品的研發,再來是從訂單取得,到涉及原料的. 備料、生產流程等程序,然後是物流管理 ... 於 nccur.lib.nccu.edu.tw -
#4.企業流程改善分析-以慶興公司為例 - 建國科技大學
SWOT 分析、有效的生產管理製程分析、接單及進出貨管理分析、品管作業分. 析、產品開發作業分析,使生產線上的工作環境、生產流程以及人員配置的整. 個工作系統能更有效率 ... 於 ir.lib.ctu.edu.tw -
#5.產品介紹
本公司擁有一貫化流程生產設備,並採用電腦控制自動化生產,以求材料品質穩定性。螺絲、螺帽等設備,則增購六模六沖成型機台、熱打成型機,增加產品外形、尺寸選擇的 ... 於 www.chunyu.com.tw -
#6.生產管理改善案 以伯知公司為例
用檢核表個案公司生產流程加以分析,以發現生產上的缺失並提出改善方法,供 ... 適用於生產產品品質一致且數量較大,為求大量生產以降低生產成本,. 於 bm.mcut.edu.tw -
#7.製作流程∣銢晟實業股份有限公司
產品生產流程 ; 5, 空壓機, 2 ; 6, 噴砂機, 1 ; 7, 振動研磨機, 3 ; 8, CNC铣床, 1. 於 www.lwp.com.tw -
#8.料管生產流程圖
南允公司專業設計生產全系列螺桿與料管, 適用於塑膠/橡膠押出機及射出成型機, ... 符合客戶的特殊應用,以確保南允的螺桿與料管能幫助客戶提升產品品質與生產效率。 於 www.nyi.com.tw -
#9.生產規劃、物流管理與決策程序
製造業的物流:產品從投入原料,製程轉換到產出,. 不斷增加價值的過程中,實體流動的過程。這中間. 包含物料流與資訊流動,對此活動進行計畫,組織,回. 於 iem.csu.edu.tw -
#10.生產流程的基本屬性 - 中文百科知識
流程 再造的定義為:“對經營程式進行根本的再思考和徹底的再設計,給運營帶來顯著的改善。”經營過程包括:產品的設計製造和管理過程。流程(Process)是指為完成某項任務而 ... 於 www.easyatm.com.tw -
#11.生產作業流程 - MBA智库百科
而且因為工廠能排出工作流程進度表,從而使造船周期大大地縮短。從這個例子可以看出,單一產品生產系統的組織與傳統的手藝行業的組織有著根本的不同。在手藝行業 ... 於 wiki.mbalib.com -
#12.新產品導入暨生產管理作業流程__臺灣博碩士論文知識加值系統
詳目顯示 ; Chen-Chuan Hsu · 新產品導入暨生產管理作業流程 · New Product Introduction and Production Control Workflow · 陳子立 · Tzu-Li Chen. 於 ndltd.ncl.edu.tw -
#13.生產流程圖 - Usyllr
13/11/2017 · 「製造」就是以規定的成本、規定的工時、生產出品質均勻、符合規格的產品。要達到上述目的,如果製造現場之作業如工序的前後次序隨意變更,或作業方法或作業 ... 於 www.huongmd365.co -
#14.研發流程| 大舜實業股份有限公司
大舜的研發流程介紹. ... 研發流程. Daysun產品RD流程 研發流程- 眼鏡 ... 在試模生產期間,QC部門將進行測試並用分析報告進行驗證,以確保產品滿足我們的初始要求。 於 www.daysungroup.com -
#15.第十九章生產計畫與管制
接單式生產係針對必須有技術能力才能製造的特殊產品,例如連結物料搬運與加工的設備,用於 ... 接單、下單、生產至交貨的流程。此種生產型態強調就近生產、供銷及 ... 於 www.taiwan921.lib.ntu.edu.tw -
#16.用IT創造彈性流程實現多樣少量生產 - iThome
然而,大訊科技脫穎而出的作法則是,利用IT實現快速交貨與多樣少量的生產模式,生產其他廠商不願生產的產品來提高競爭力。 於 www.ithome.com.tw -
#17.生產流程改善與優化方法有哪些 - 今天頭條
因此,必須把「出錯保護」的思想貫穿整個生產過程,保證每一種產品只能嚴格地按照正確的方式加工和安裝,從而避免生產流程中可能發生的錯誤。 於 twgreatdaily.com -
#18.新產品開發流程之探討 以車燈製造公司為例The Research of ...
之檢討,填寫新產品企劃案分析(聯絡單),再決. 定開發與否;POG 309 經審核其物料成本、模具費. 用及製造成本分析與開發、生產技術皆為該個案公. 於 www.feu.edu.tw -
#19.生產流程 - 金居開發股份有限公司
金居生產「電解銅箔」提供銅箔基板、多層印刷電路板、高密度連接板電鍍的添加等關鍵材料;並期許提供使顧客滿意的客製化產品。 於 www.co-tech.com -
#20.NSYSU_93-生產與作業管理CH5:產品設計與製程選擇
5 主要功能部門的作業流程市場需求生產製造行銷與銷售產品開發製造行銷進階研究製程生產規劃顧客產品市場系統設計銷售 推廣 顧客訂單 拜訪 新產品 創意 生產訂單 產品 ... 於 slidesplayer.com -
#21.模具生產流程- 慶穗 - 精密塑膠射出工廠
模具設計與討論. 階段. 2. CNC加工. 階段. 3. EDM放電加工. 階段. 4. 合模. 階段. 5. T1試模. 階段. 6. T1試模討論. 階段. 7. 模具拋光. 階段. 8. T2試模與產品確認. 於 www.chingsui.com -
#22.生產流程 - 日翔軟板科技股份有限公司
生產流程 產品 與技術/ 生產流程. 單面軟板製造流程. 雙面軟板製造流程. 多層軟板製造流程. Copyright © 2021. 日翔軟板科技股份有限公司. All rights reserved. 於 www.jtflex.com.tw -
#23.製程能力- 製造流程 - 韻翔國際有限公司
韻翔國際有限公司成立於1978年為電子相關產品之OEM專業加工廠。營業項目包含PC板加工、 ... 有計劃的給予生產人員教育訓練,製程SOP、品質教育,以達到最佳品質標準。 於 www.innoflux.com.tw -
#24.第二章.產品生產流程介紹- 工作研究報告 - Google Sites
第二章.產品生產流程介紹. 第三章:作業程序圖 · 第五章:改善方案(程序分析) · 第六章:總結 · 第四章:改善方案(作業分析) · 協作平台地圖. 第二章.產品生產流程介紹 ... 於 sites.google.com -
#25.以二階式生產流程模式構建半導體封裝現場流程管制系統
本文依製造. 料表的觀念提出二階式生產流程模式(Two-. Layer Manufactur in Process Model),其構. 建包括:(1) 上階的工單製程、產品製程:透. 過晚期客戶化(Late ... 於 ir.nctu.edu.tw -
#26.生產流程卡-新人首單立減十元-2022年4月 - 淘寶
工廠產品流動標識卡車間工藝流程卡物料卡流轉卡生產工序單 ... 工廠通用車間生產工序流程卡工藝流轉卡產品物料標識卡合格不良品庫存卡存料卡表單吊牌紙卡印刷現貨包郵. 於 world.taobao.com -
#27.如何做好生產線管理提升企業競爭力(以製造業為例)
企業的生產線是企業生產能力的載體,生產線的作用從某種程度上來說是整個 ... 材料延誤入廠無所謂反正可立即改生產其他產品、同產品不同人員生產其 ... 於 mymkc.com -
#28.排程與生產作業控制
連續式生產與大量生產:單一產品⇒生產線平衡(assembly line balancing). 多種產品⇒批量及JIT ... 流程型態. 評估法則. 2. 零工式排程的目標. 趕上期限. 使WIP 最少. 於 dstm.ntou.edu.tw -
#29.淺談開發流程的品質控管
P6. 量產前之準備檢討。 完成各項生產必備之文件。 針對產品殘留問題進行檢討與對策。 專案負責人,研發設計人員,生物管人員,工程人員,製造人員,品保人員 ; P7. 進入量 ... 於 sabrina0823.pixnet.net -
#30.產品製造 - 緯創
緯創的資訊系統透過生產排程者、零件供應商及客戶間有效率的合作而能提供接單後生產(BTO)及客製化生產(CTO)的運作模式,為BTO及CTO產品所計劃的周轉期是透過有系統的流程 ... 於 www.wistron.com -
#31.生產流程 - 英易生技有限公司
英易相信;唯有嚴格的原物料檢驗,才能生產出完美的產品。 Step.3 瓶器消毒. 針對瓶器材質、印刷方式及包裝方式.. 於 www.inyi.com.tw -
#32.貳、作業流程分析(農委會) - 行政院農業委員會
瞭解產品的物料組合,減少生產誤差及損耗。 瞭解物料的特性,有助於生產流程的安排,使作業更加順暢。 作法二、產品組合圖:參考 ... 於 www.coa.gov.tw -
#33.範例1.產品製造流程圖(僅供參考) (1)產品名稱
產品 製造流程圖(僅供參考). (1)產品名稱:○○○○○. (2)主要產品製造流程. 原紙入料. 貼合、壓楞. (公告製程). 貼合機:. 五層瓦楞紙製造機. 於 www.cto.moea.gov.tw -
#34.產品方案-智能製造-生產管理|天心資訊
生產管理系統是透過智慧分析作業,自動計算生產相關數據,精準掌控用料成本避免浪費,簡單高效控制生產 ... 簡易生產,從而簡化了企業生產流程又可做到工序的管理。 於 www.attnerp.com.tw -
#35.生產流程 - 燁輝企業股份有限公司
產品 相關: [email protected]. 人才招募: [email protected]. 其他問題: [email protected]. Copyright © 2022 燁輝企業股份有限公司版權所有. 於 www.yiehphui.com.tw -
#36.縮生產流程減缺陷 品牌製人偶宣傳
香港科技園公司企業拓展及科技支援副. 總裁楊德斌看好3D打印,認為有助港. 商縮減生產模辦時間及成本。「廠商以. 前託內地廠房造一個產品原型要2至4星. 於 www.hkpc.org -
#37.基本觀念
生產設備依照產品的生產流程配置,每一工件按順序流經各生產設備。工件的途程(Route)是固定的,因為不論何種工件均按一定的途程作業,所以工件之間 ... 於 www.kimas.com.tw -
#38.五、生產型態
批量生產(Batch Production):. 產品的種類很多,但同一個批次的產量卻相對較少。 同樣的產品在不同的期間亦可能重複受訂。 機械工廠(Job Shop)均為此種生產 ... 於 publish.get.com.tw -
#39.消失的國界-賀寶芙產品生產流程報導2012-4-21 - YouTube
賀寶芙 產品 從種子裁種到 產品 研發製造,每一個 流程 都經過層層嚴格把關,用最頂尖高端的科技萃取最優質的細胞營養食品,讓我們每天都吃的安心又健康~^0^ ... 於 www.youtube.com -
#40.ODM 模式下之網路通訊產品設計程序研究
以現今全球市場上的產品研發及生產現況來看,比起以往3C 科技產業的設 ... 設計流程的執行上也被逼迫轉變;就公司開發團隊及產品工程師而言,實是有. 於 rportal.lib.ntnu.edu.tw -
#41.實踐技巧提高您的生產效率 - Arburg
流程 控制. 企業的成功並非意外。生產效率極為重要!並且這體現在整個價值. 創造鏈上——從開始的產品設計到生產計劃,包括比如能源管理或. 相應的企業戰略等上層影響因素 ... 於 www.arburg.com -
#42.如何設計產品的生產流程卡 - 台部落
各位朋友同仁,大家好! 我所在的公司是電鍍廠,屬於來料加工企業. 因爲客戶多,產品多,鍍種不同,基本生產管理和計劃管理的需要,並做到後續有據可查, ... 於 www.twblogs.net -
#43.生產流程| 熯錩實業有限公司
熯錩擁有經驗豐富、技術精良的技師與熟悉英、日語言的業務人員可以針對顧客的需求即時討論,我們的專業團隊了解各類製程、產品加工細節及不同製程的生產轉換,並依照 ... 於 www.hcintalm.com.tw -
#44.電子產品生產流程相關名詞 - 拾人牙慧
... 電子產品生產流程相關名詞Kickoff - 專案正式開案,時間上不一定在. ... Gerber out - PCB 廠用來生產PCB 時需要的檔案,通常可以由Layout 軟體 ... 於 silverwind1982.pixnet.net -
#45.YCC產品生產流程補充說明
生產流程 · YCC產品生產流程補充說明 · O-RING 產品物性表 · 油壓密封件材質物性表 · 空壓密封件材質物性表 · TPU (PLOYURETHANE ) 材質物性表 ... 於 www.ycc.com.tw -
#46.生產流程 - 明嘉生物科技有限公司
常用於防止產品粉末飛散,改善流動性,增加保存性和粉末填充的定容量。 濕式造粒機Wet Granulator. 將快速混合後加溼的 ... 於 www.mingjia.com.tw -
#47.服務生產流程介紹| 興化成包裝實業有限公司 - CENTROPAK
興化成塑膠容器的服務生產流程介紹. ... 我們的產品以主要是各類食品容器,射出成型/真空成型的各式塑膠容器,包括PP微波冷凍封口盒、布丁果凍杯、保鮮盒等, ... 於 www.centropak.com.tw -
#48.獨家一貫化生產製程- 恒升企業服務流程
恒升企業獨家一貫化生產製程,從產品設計、生產、製造到後加工,全程獨立完成有效掌握品質,即時追蹤交期,讓你最踏實、放心的專業板金企業。 於 www.heson.com.tw -
#49.生產流程| 萬乘實業股份有限公司
萬乘擁有經驗豐富、技術精良的技師與熟悉各國語言的業務人員可以針對顧客的需求即時討論,我們的專業團隊擁有超過30年的製造經驗,了解各類製程、產品加工細節及不同製程的 ... 於 www.wassheng.com.tw -
#50.生產流程- 產品介紹
回首頁 > 產品介紹 > 生產流程. 生產流程. 回上頁. 鑫辰鋼鐵股份有限公司北部分公司新北市板橋區大觀路一段28巷112號TEL:(02)2967-9068 鑫辰鋼鐵股份有限公司屏東縣屏 ... 於 www.xc-steel.com.tw -
#51.矽膠產品生產工藝流程 - 壹讀
矽膠產品的生產流程有哪些? 矽膠產品的成型工藝分為兩種:一種是固態熱壓硫化成型,另一種是液態打針成型。 ... 今天矽膠製品工廠貝智特矽膠小編著重 ... 於 read01.com -
#52.生產流程 - KingLab 金永德實驗室設備有限公司
生產流程. 產品自生產的每個流程,從小細節都不放過,因為是從設計→製造生產,產品安裝→試俥等等都是由工廠一體化製作,因此可以嚴格的管控交期及產品的品質。 於 www.kinglab.com.tw -
#53.流程製造都有哪些生產特徵 - 好問答網
4)生產過程中常常出現聯產品、副產品、等級品。 三、過程分解分析. 將流程生產過程進行這樣分解:把要生產加工物料的過程分解成各個邏輯階段,每個 ... 於 www.betermondo.com -
#54.生產流程-二億企業股份有限公司
採用自動化生產設備與一貫標準流程,織帶卓越品質值得客戶信賴! 01原料 02前置加工 03織造 04染整 05後加工 06品檢 07包裝 08入庫 09出貨. 於 www.ecigroup.com.tw -
#55.產品生產流程 - 1wiuu
生產 作業流程.ppt,生產作業流程管控生產制程與服務的流程﹐熟悉生產管理的各階段作業產品從計劃排程到產品出貨的各個階段品質活動均需進行管控品保負責產品的檢驗與不合格 ... 於 www.1wiiu99.co -
#56.產品(服務)流程(過程)管理支援性活動管理跨組織關係管理
產品流程 管理-管理系統架構. 支援性活動. 智權管理. 生產技術. 品質管理. 資訊管理. 財務管理. 人力資源. 物料管理. 採購管理. 跨組織管理. 導入評選. 品質評定. 於 nqa.cpc.tw -
#57.產品製造流程
產品 製造流程 ; 將材料預熱後再予成形,成形品硬化狀況均勻,提高品質安定性 ; 高溫高壓成形生產 ; 在大型成形機中以1c㎡約200kg的高壓成形,表面硬度均勻,不容易有損傷或 ... 於 www.melamine.com.tw -
#58.工廠生產流程圖 - Merisa
米粉生產流程圖攪拌、蒸氣加熱至半熟儲存桶低型壓迫機高型壓迫機繁中EN 日本語X 關於華益核心能力專業製造生產流程品質控管銷售區域專業驗證主要客戶產品介紹. 於 www.grapplrts.me -
#59.電子產品生產工藝流程 - 每日頭條
2017年6月3日 — 生產流程如下: · 1)採購進廠的元器件經進貨檢驗後進入元器件倉管理。 · 2)生產計劃排出後按計劃將元器件發給整形部門,對元器件、印製板進行整形,做好 ... 於 kknews.cc -
#60.喬勝機動車配件有限公司- 生產流程介紹
生產流程 介紹. 工作區域 1. 工作區域 2. 工作區域 3. 工作區域 4. 工作區域 5. 產品交期大概多久? 返回列表. 常見問題分類. 產品應用知識 · 產品相關服務 ... 於 www.njk.com.tw -
#61.好食好事基金會- 不同於一般產品生產流程 - Facebook
不同於一般產品生產流程,不花費很長的的開發製作。 Prototype利用最短的時間做出雛型後,進行市場可行性測試。 當市場反應良好時,即可投入更多的資金並修改改良成更 ... 於 www.facebook.com -
#62.產品製作流程 - 蓮花工業股份有限公司
開模. Molding. 原料(鋁擠錠). Al Ingot Prep. 鋸錠. Slicing the Ingot. 擠壓. Extrusion. 時效. Aging. 製成檢查. Process Check. 於 adinfi.com.tw -
#63.製造流程 - 俊來金屬股份有限公司
當客戶向業務單位提出非標準量產之規格訂單後,研發單位將依據產品圖樣研擬製造程序並開發專用模具,同時亦與品管人員協商新製程之檢驗內容與方式。一旦產品試作完成,我們 ... 於 www.junelai.com.tw -
#64.生產流程 - 立宇高新科技股份有限公司
液晶電視塑殼產品 · AIO電腦塑殼產品 · 電聲塑殼產品 · 網通塑殼產品 · 生產流程 · 模具設計製造 · 產品成型製造 ... Home; 生產流程. ▻ 生產流程 ... 於 www.liyuep.com.tw -
#65.建立及管理製程計劃
它們包含要執行的作業、必須完成作業的順序、實體資源、必要的工廠與技能、文件參考、文字描述及時間與成本需求。 使用製程計劃,您可以定義:. • 執行產品製造工作所需要 ... 於 support.ptc.com -
#66.優勢與特色| 全面性一站式服務,從概念到批量生產的完整流程
多樣化的製造和技術服務. 為客戶提供從產品概念到物流交付的全方位服務,包含概念設計、產品設計、製作試樣、小批量生產、驗證、量產。 於 www.charder.com -
#67.生產流程一貫化 - 久慶塑膠股份有限公司
生產流程 一貫化. ... 秉持著品質第一、交貨第一,服務第一的「三一品質政策」,久慶對產品的品質控管極為嚴格。除要求設備定期保養,也落實整理、整頓、清掃、清潔、 ... 於 www.chew.com.tw -
#68.「新產品開發流程」與「產品創新」的關連性 - SmartM 人才 ...
在宏碁,產品經理宛如產品的總經理,決定產品的生與死(退出市場);從市場需求的評估、產品規格的發想,到最後經由研發、生產、行銷等部門的催生,及至 ... 於 www.smartlinkin.com.tw -
#69.「建立標準生產流程」找工作職缺-2022年5月|104人力銀行
大學. 產品之生產維護及改善(車用/健身/戶外/航空/航海產品): 1.標準工時的建立與維護。 2.制訂製造程序與作業標準(SOP)。 3.持續產品與製程改善,提升生產效率與產能 ... 於 www.104.com.tw -
#70.產品生產流程說明| 良冠生化科技有限公司 - BIOCROWN
良冠的產品生產流程說明. 從1977年以來,良冠生化科技不斷尋找天然成分、研發有效配方與創新科技結合,為創造肌膚美麗事業為宗旨而不斷傳承下去。 於 www.biocrown.com.tw -
#71.水產品生產流程圖譜:史氏鱘 - 博客來
書名:水產品生產流程圖譜:史氏鱘,語言:簡體中文,ISBN:9787546313436,頁數:105,出版社:吉林出版集團有限責任公司,作者:夏艷潔,出版日期:2010/03/01, ... 於 www.books.com.tw -
#72.生產設備 敏軒企業有限公司Min Hsuan Enterprise Co., Ltd.
生產流程 · 模具製作流程. 圖面接收. 討論及尺寸確認. CAD模具設計. 材料訂購. 線切割&CNC加工模具. 螺絲孔、彈簧孔加工&組立. 試模 · 產品生產流程. 客戶訂單. 生產排程. 於 www.contool.com.tw -
#73.生產流程- 產品介紹 - 良豪工業股份有限公司
生產流程. 首頁 · 產品介紹 · 生產流程 · 鋼種 · 產品規格 · 生產流程 · 終端產品. Step. 1. 抽伸. Step. 2. 矯直+QC. Step. 3. 倒角. Step. 4. 浸油+包裝. Step. 5 ... 於 www.lion-hower.com.tw -
#74.生產流程Production process - ASCARE FoodStuffs Co.,Ltd. 亞 ...
一個完美且高品質的產品,需要有最好的原物料、菁英的研發團隊、專業技術人員、精良的機器設備,以及精密檢驗儀器,生產滿足客戶所需的產品,是亞世佳食品股份有限公司 ... 於 www.ascarfood.com.tw -
#75.【生產與作業管理 ~ 】講義 - 鼎文公職
將土地、勞動、機器設備、原材料、能源等生產資源投入,. 經過加工或製造等轉換程序,可產生瞭種產品或服務,以滿足人分慾望,提供人們效用。 所謂生產管理,係指將管理 ... 於 www.ting-wen.com -
#76.中國西部水泥有限公司- 產品簡介> 生產流程
水泥的生產過程分為四個主要階段:(1)原材料破碎;(2)原材料煅燒及混合;(3)熟料燒結;及(4)研磨混合熟料,製成水泥。 原材料破碎. 我們將石灰石、石膏、粘土、粉煤灰、硫 ... 於 www.westchinacement.com -
#77.生產流程- 產品介紹 - 精冶科技工業股份有限公司
產品 介紹. 首頁; 產品介紹. 木型檢修. 砂模製作. 合模. 熔解. 退火爐. 洗砂機. 1. 產品分類. 生產流程 · 品質檢驗設備 · 鑄鐵鑄件 ... 於 www.ginyeh.com -
#78.製造與服務 - 得洋電子
新產品導入流程. 規劃完整的生產日程計劃,包含準確進料、測試、會議討論、組裝時間,依ISO-9001規範,擬定品質管制相關書面作業程序文件以及製程管理程序(採購管制、 ... 於 www.dynatron.com.tw -
#79.作業管理 - 朝陽科技大學
產品 設計與製程選擇-製造業 ... 產品/流程工程:產品及設備之設計、原型製作與測 ... 試產與量產:量產分析、工廠開始生產、產量漸增至量. 於 www.cyut.edu.tw -
#80.生產流程| 德利威電子股份有限公司 - DAILYWELL
組裝過程中依《作業標準書》製程作業執行,並依《品質檢驗管制程序》管制執行,確保作業及產品品質。 所有訂單均有ERP記錄,便於追朔及查詢。 生產流程 ... 於 www.dailywell.com.tw -
#81.如何有效管理生產品質百佳泰就是不一樣! - Technical Direct
IPQC (In Process Quality Control) – 製程品質管理:檢驗內容從投入物料生產到產品最後包裝,整段流程包含以下項目:. 1. 稽核生產線上各生產站別,例如 ... 於 www.technical-direct.com -
#82.一个实体产品从无到有,过程是怎样的?设计过程是怎样的 - 知乎
每个部分的工作,都有各自不同的流程和方法,就不一一表述了。设计结束后,需要做出可工作的工程样机。这个样机,90%以上和最后的量产机一样,只是生产的方式不同而已 ... 於 www.zhihu.com -
#83.制造业- 维基百科,自由的百科全书
現代的製造業包括了所有配合生產需求的半成品製程以及整合產品各部份的集成製造流程,涵蓋的領域與工程及工業設計之間有著密切的協作關係。在各種類型的經濟體制和系統 ... 於 zh.wikipedia.org -
#84.笨槑的產品生產流程&不負責解析 - 麻衣大
笨槑今天"再度"公開(以前也有過但沒這次詳細) 產品的生產流程影片是生肉..影片字幕給他點自動翻譯意思不會差很多! 主要還是為了盜版的問題追加新式的 ... 於 mai10281106.pixnet.net -
#85.生產流程簡介| 輝庭企業股份有限公司 - Huei Tyng
成品線上包裝前須依據【成品檢驗標準】確認物料尺寸再組裝首件;依產品類別,以棧板為單位於上張貼成品吊卡標示,以期產品都能完美交到客人手上。 物料入庫定位時,須做好 ... 於 www.hueityng.com.tw -
#86.生產流程 - 正慧食品工業股份有限公司
生產流程. 正慧公司採用全自動一貫作業,從進口原料的選用、產品的研發測試、填充成型、產品包裝、到高效率的運送服務,無時不以滿足客戶使用為最高原則。 於 www.hnc-chocolate.com.tw -
#87.流程管理專欄— 認識產品開發流程
量產階段(Production): MP活動:「貼片製程、插件製程、產品組裝、產品初終測、產品包裝…」 OP活動:「技術 ... 於 adaptive.com.tw -
#88.ODM流程介紹:: 台灣尖端科研生醫有限公司| 產品開發、產品設計
客戶接洽 · 了解客戶需求 · 品牌設計與行銷企劃提案 · 研發打樣 · 客戶樣品確認 · 生產製造 · 品管檢驗 · 包材設計. 於 taiwantsrb.com -
#89.Chap 1 生產系統與計畫管制
輸入轉換為產品或服務的流程。 ▫ Manufacturing is the production of tangible goods (products). Manufacturing is the transformation of raw materials into products ... 於 ocw.nthu.edu.tw -
#90.基本要素,基本屬性,流程再造,生產流程改進 - 中文百科全書
生產流程 ,又叫工藝流程或加工流程,是指在生產工藝中,從原料投入到成品產出,通過一定的設備按順序連續地進行加工的過程。也指產品從原材料到成品的製作過程中要素的 ... 於 www.newton.com.tw -
#91.流程型製造業的工業4.0 應用
我們先前介紹Industry 4.Now 是SAP 為企業客戶帶來的可落地、可實踐的工業4.0 策略。這個策略以生產型企業的價值鏈出發,串聯產品最初的研發創新到客戶購買後的維護 ... 於 news.sap.com -
#92.生產流程_百度百科
生產流程 ,又叫工藝流程或加工流程,是指在生產工藝中,從原料投入到成品產出,通過一定的設備按順序連續地進行加工的過程。也指產品從原材料到成品的製作過程中要素的 ... 於 baike.baidu.hk -
#93.產品製造介紹| 倡明電機有限公司
生產流程 圖文件下載 · 交流(AC) · 直流(DC) · 線材(WIRE) ... 於 www.cmec.com.tw -
#94.作業流程分析
分析流程的第一步是一個非常困難、但很重要的問題,清楚. Page 5. 第三篇產品的設計與製程的選擇. 87. 地定義分析流程的目的何在?是去解決一個問題?或是了解變革對企. 業 ... 於 tutorial.bm.nsysu.edu.tw -
#95.產品開發流程的6 個階段(附有範例)
到目前為止,您已經完成了開發與行銷策略的設計和品質測試。您應該對最終的迭代成果充滿信心,並準備好生產最終產品。 您將在此階段中進行下列事項:. 於 asana.com -
#96.SportsArt 生產流程認證- 卓越的簡介
SportsArt 是業界擁有最為垂直整合生產流程的製造商之一,從設計到產品組裝一條龍式全部掌握。 · SportsArt 自行生產製造80%以上的產品零件,並符合ISO 9001、ISO13485及 ... 於 www.gosportsart.com